Operating Specifications and Precautions for Thermal Shock Test Machine
Published: 7/7/2025
5 min read
The thermal shock test machine is used to simulate the thermal shock resistance of materials in environments with rapid temperature changes and is widely applied in the research and quality inspection...
Article Content
The thermal shock test machine is used to simulate the thermal shock resistance of materials in environments with rapid temperature changes and is widely applied in the research and quality inspection fields of ceramics, metals, composites, and other materials. Proper operation of the equipment is key to ensuring the reliability of test results and extending the lifespan of the equipment. 1. Equipment Composition and Working Principle 1.1 Equipment Composition The thermal shock test machine mainly consists of the following parts: - Heating system: includes a high-temperature furnace and temperature controller for rapid heating of samples. - Cooling system: typically uses compressed air or water cooling devices for rapid cooling of samples. - Sample holder: used to secure the sample, ensuring its position remains stable during heating and cooling. - Temperature sensor: monitors the temperature changes in real-time for the furnace and sample. - Control system: sets heating/cooling programs, records temperature curves, and controls the testing process. 1.2 Working Principle By setting alternating cycles of high and low temperatures, the machine simulates the sudden temperature changes that materials experience in actual use. For example, the sample is heated to a set temperature (e.g., 800°C) and then rapidly cooled (e.g., using compressed air to cool to room temperature) to observe whether the material cracks or is damaged, thus evaluating its thermal shock resistance. 2. Usage Steps and Operating Specifications 2.1 Preparation Before Testing - Sample Preparation: The sample size must meet the equipment requirements (e.g., cube, cylinder, etc.), and the surface should be clean and free of cracks. Measure the sample dimensions with calipers and record the original data. - Equipment Check: Ensure the heating furnace and cooling system are functioning properly and that the temperature sensor is sensitive. Verify that the compressed air pressure or water flow meets equipment requirements. Clean the sample holder to avoid residual material affecting test results. 2.2 Setting Test Parameters - Temperature Range: Set the heating temperature (e.g., 500°C to 1500°C) and cooling temperature (e.g., room temperature or low-temperature bath) according to material characteristics. - Holding Time: Set the high-temperature holding time (e.g., 5 minutes) to ensure uniform internal temperature of the sample. - Cooling Rate: Choose the cooling method (e.g., compressed air, water cooling, or natural cooling) and set the cooling time. - Number of Cycles: Set the number of thermal shock cycles (e.g., 1 to 100) based on test requirements. 2.3 Testing Procedure - Sample Installation: Secure the sample in the sample holder, ensuring it is aligned with the heating source and cooling system. - Start Heating: Heat the sample to the target temperature according to the set program, monitoring the temperature curve. - Rapid Cooling: After reaching the holding time, start the cooling system (e.g., turn on compressed air) to quickly lower the sample temperature. - Cycle Testing: Repeat the heating-cooling cycle until the set number of cycles is reached. - Observation and Recording: After each cycle, check the sample surface for cracks and record the cycle count and temperature changes when cracks appear. 2.4 Post-Test Processing - Sample Inspection: Remove the sample and observe the crack distribution under a microscope, taking photographs for records. - Data Organization: Export temperature curves, cycle counts, and other data to generate a test report. - Equipment Cleaning: Clean the furnace, sample holder, and cooling system to prevent residual material from affecting subsequent tests. 3. Precautions and Safety Regulations 3.1 Safety Operations - Wear protective gloves and goggles to avoid burns from high temperatures or splashes from cooling media. It is strictly prohibited to open the furnace or cooling system while the equipment is running to prevent high-temperature gases or liquids from spraying out. 3.2 Equipment Maintenance - Regular Calibration: Use a standard thermometer to calibrate the temperature sensor to ensure measurement accuracy. - Cooling System Check: Regularly clean the compressed air pipes or water cooling system to prevent blockages. - Heating Element Protection: Avoid direct contact between the sample and heating elements to prevent short circuits or damage. 3.3 Control of Testing Errors - Temperature Uniformity: Ensure even temperature distribution within the furnace to avoid local overheating or overcooling. - Stable Cooling Rate: Adjust the flow rate of the cooling medium to maintain consistent cooling rates for each cycle. - Sample Consistency: Use samples of the same size and material for the same set of tests to reduce variable interference. The thermal shock test machine is an important tool for evaluating the thermal shock resistance of materials, and its operation must strictly follow specifications with attention to detail control. By reasonably setting test parameters, standardizing operating procedures, and regularly maintaining equipment, the accuracy and reliability of test results can be effectively improved while extending the equipment's lifespan. Mastering the above usage instructions not only ensures smooth testing but also provides a scientific basis for material development and quality control.
Original Article
This article was originally published on our Chinese website. You can view the original version below:
View Original Article →Contact Us for More Information
Have questions about our products or services? Get in touch with our team for expert assistance.
Send us a Message
Contact Information
- Phone
- Office
- Fax
- Address
B6-101, Zhongnan High-Tech Intelligent Manufacturing Industrial Park, No. 10 Shuangma Street, Yuetang District, Xiangtan City, Hunan Province, China
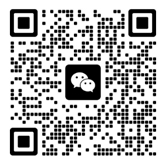