Detailed Explanation of the Usage Method and Key Points of Refractory Material Testing Equipment
Published: 6/12/2025
4 min read
In the research and development, production, and quality control of refractory materials, the refractory material testing equipment is an important tool. It can simulate high-temperature environments ...
Article Content
In the research and development, production, and quality control of refractory materials, the refractory material testing equipment is an important tool. It can simulate high-temperature environments to accurately test key properties of refractory materials such as thermal stability, compressive strength, and flexural strength. Below is a detailed analysis of the usage method of the testing equipment and key points during the operation process. 1. Introduction and Principle of the Testing Equipment This is a comprehensive testing device that integrates heating, loading, measurement, and control. Its working principle is to provide a stable high-temperature environment through a high-temperature furnace while using a loading system to apply pressure or tension to the sample. The measurement system records data such as the deformation of the sample and the magnitude of the load, thereby calculating the mechanical performance indicators of the material. This process is significant for evaluating the high-temperature performance, thermal shock resistance, and service life of refractory materials. 2. Usage Method and Steps 1. Sample Preparation: Prepare samples that meet specifications according to testing standards or requirements. The samples should be representative, accurately sized, and have a smooth surface without cracks. Additionally, perform pre-treatment on the samples, such as drying and cleaning, to ensure the accuracy of the test results. 2. Equipment Inspection and Preheating: Before the test, conduct a comprehensive inspection of the refractory material testing equipment, including the heating system, loading system, measurement system, and control system. After ensuring the equipment is in good condition, start the heating system for preheating to reach the required temperature for the test. 3. Sample Loading and Fixing: Place the prepared sample on the supporting device of the testing equipment, adjust its position to ensure it is aligned with the loading device. Then, use clamps or fixing devices to securely hold the sample in place to prevent displacement or falling during the test. 4. Parameter Setting and Test Start: Set the heating temperature, loading speed, measurement range, and other parameters of the testing equipment according to the test requirements. After confirming the settings are correct, start the testing equipment to begin the test. During the test, monitor the temperature inside the furnace, the deformation of the sample, and the magnitude of the load in real-time. 5. Data Recording and Processing: After the test, remove the sample from the testing equipment and record information such as the fracture load, fracture location, and fracture characteristics. At the same time, calculate the compressive strength, flexural strength, and other mechanical performance indicators of the sample based on the measurement data. By comparing the test results of different samples, analyze the performance differences of the refractory materials and their influencing factors. 3. Key Points and Precautions 1. Safety Operation: During the test, strictly adhere to safety operating procedures, wear protective equipment, and avoid burns from high temperatures or mechanical injuries. Also, ensure the testing environment is well-ventilated to prevent the accumulation of harmful gases. 2. Temperature Control: During heating, strictly control the temperature to avoid adverse effects on the sample from temperatures that are too high or too low. Maintain a stable temperature to ensure the accuracy and repeatability of the test results. 3. Loading Speed: The loading speed should be moderate; too fast may cause the sample to break due to impact, while too slow may cause the sample to soften from prolonged exposure to high temperatures. Choose an appropriate loading speed based on the test requirements. 4. Data Accuracy: During the test, accurately record all data, including the deformation of the sample, the magnitude of the load, and the temperature. This data is the basis for subsequent analysis, and its authenticity and accuracy must be ensured. 5. Equipment Maintenance: Regularly maintain and service the refractory material testing equipment, such as cleaning the equipment, checking fasteners, and lubricating moving parts. Also, periodically calibrate and verify the equipment to ensure its measurement accuracy and stability. The usage method of the refractory material testing equipment involves multiple links and key points. By correctly operating and maintaining the equipment, one can accurately assess the performance indicators of refractory materials, providing strong support for the research and development, production, and quality control of refractory materials.
Original Article
This article was originally published on our Chinese website. You can view the original version below:
View Original Article →Contact Us for More Information
Have questions about our products or services? Get in touch with our team for expert assistance.
Send us a Message
Contact Information
- Phone
- Office
- Fax
- Address
B6-101, Zhongnan High-Tech Intelligent Manufacturing Industrial Park, No. 10 Shuangma Street, Yuetang District, Xiangtan City, Hunan Province, China
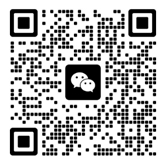