How to Maintain and Calibrate a Laser Thermal Conductivity Meter?
Published: 4/10/2025
4 min read
Here are the detailed methods for maintaining and calibrating a laser thermal conductivity meter: 1. Daily Maintenance 1. Cleaning (1) Cleaning Optical Components: The optical components of ...
Article Content
Here are the detailed methods for maintaining and calibrating a laser thermal conductivity meter: 1. Daily Maintenance 1. Cleaning (1) Cleaning Optical Components: The optical components of the thermal conductivity meter, such as the laser window and lenses, are easily contaminated by dust and oil. They should be gently wiped regularly (for example, once a week, with the specific frequency adjustable based on the usage environment) using clean, lint-free cotton or lens paper. For stubborn stains, a small amount of anhydrous ethanol can be used for wiping, but care must be taken to avoid liquid seeping into the internal optical components and causing damage. (2) Cleaning the Sample Stage: After each use, residual materials such as debris and dust from the test materials on the sample stage should be cleaned. If the samples are corrosive or volatile, they should be cleaned promptly to prevent corrosion of the sample stage or affecting results in the next test. 2. Environmental Control (1) Temperature and Humidity: The laser thermal conductivity meter should be placed in an environment with suitable temperature and humidity. Generally, a temperature of 18-25°C and a relative humidity of 40%-60% are ideal. Avoid exposing the instrument to moisture, as humidity can cause rusting and short-circuiting of electronic components; also, do not expose the instrument to high temperatures to avoid affecting its performance and lifespan. (2) Dust Prevention: The instrument should be placed in a clean, low-dust environment. If the laboratory or usage environment has a lot of dust, consider using a dust cover to reduce dust contamination when the instrument is not in use. 3. Mechanical Component Inspection (1) Sample Installation Parts: Regularly check the sample installation devices, such as clamps and lifting platforms, for flexibility. If any sticking or looseness is found, they should be tightened or lubricated in a timely manner. For example, check the screws of the sample clamp for looseness quarterly, and if necessary, add an appropriate amount of lubricant to ensure normal operation. (2) Connection Cable Inspection: Check the power cables, signal cables, and other connection cables for damage or aging. Replace any problematic cables promptly to ensure the electrical safety of the instrument and normal communication. 2. Calibration Methods 1. Standard Sample Calibration Method (1) Selecting Appropriate Standard Samples: Choose certified standard samples based on the measurement range and application needs of the thermal conductivity meter. For example, for instruments measuring the thermal conductivity of solid materials, select standard metal blocks or ceramic blocks with known and high-accuracy thermal conductivity values. (2) Testing Standard Samples and Comparing Data: Place the standard samples in the instrument according to the normal testing procedure for testing. After obtaining the test results, compare them with the thermal conductivity values given for the standard samples. If there is a deviation, adjust the relevant parameters of the instrument (such as laser power, sample thickness correction factor, etc.) according to the instrument's operation manual to reduce the deviation and align the test results with the standard values. Generally, the required error after calibration should be within a certain range, such as not exceeding ±1%. 2. Reference Instrument Comparison Calibration Method (1) Preparing Reference Instruments: If conditions permit, use another calibrated and more accurate thermal conductivity meter of the same type as a reference instrument. Alternatively, use other reliable thermal property measurement devices, such as guarded hot plate thermal conductivity testers. (2) Synchronous Testing Comparison: Use the thermal conductivity meter to be calibrated and the reference instrument to test the same sample simultaneously. Compare the test results of the two instruments; if there are differences, adjust the parameters of the instrument to be calibrated to bring its results closer to those of the reference instrument, achieving consistency within the allowable error range. 3. Temperature Calibration (for thermal conductivity meters with temperature measurement functions) (1) Using Temperature Standard Sources: Utilize high-precision temperature standard sources, such as Class II standard platinum resistance thermometers. Contact the temperature sensor (such as thermocouples or RTDs) with the standard temperature source, and compare the temperature value displayed by the instrument with the standard temperature value. (2) Adjusting Temperature Parameters: If there is a temperature display deviation, enter the temperature settings menu of the laser thermal conductivity meter, adjust the temperature compensation parameters, or perform linear correction to ensure the temperature displayed by the instrument matches that of the standard temperature source. This step is crucial for accurately measuring material properties such as specific heat capacity and other temperature-related thermal properties.
Original Article
This article was originally published on our Chinese website. You can view the original version below:
View Original Article →Contact Us for More Information
Have questions about our products or services? Get in touch with our team for expert assistance.
Send us a Message
Contact Information
- Phone
- Office
- Fax
- Address
B6-101, Zhongnan High-Tech Intelligent Manufacturing Industrial Park, No. 10 Shuangma Street, Yuetang District, Xiangtan City, Hunan Province, China
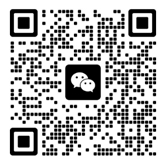