Testing the Thermal Conductivity of Carbon Felt and Other Insulating Materials Below 1600°C Using a Vacuum High-Temperature Thermal Conductivity Meter
Published: 12/16/2024
4 min read
The thermal conductivity of materials is an important parameter for studying the physical properties of materials. In industries such as aerospace, atomic energy, construction materials, and non-metal...
Article Content
The thermal conductivity of materials is an important parameter for studying the physical properties of materials. In industries such as aerospace, atomic energy, construction materials, and non-metallic materials, there is a requirement to predict or measure the thermal conductivity of relevant materials. The testing methods are divided into steady-state and dynamic testing methods. For carbon fiber materials, the testing method is based on the principle of the heat flow method, combined with the water flow plate method. An imported high-temperature heat flow sensor is used in a high-temperature vacuum environment that can also allow protective gas, with the testing work automatically completed by a computer, and each state point displayed digitally. Manual testing is also possible, meeting the high-precision testing requirements of material testing research departments and carbon material manufacturers for the thermal conductivity coefficient of materials. The instrument reference standards are GB/T 10295-2008 and YB/T 4130-2005. The parameters required for the instrument and equipment used are: 1. Heat surface temperature or furnace temperature: 600°C - 1600°C 2. Thermal conductivity testing range: 0.01 - 5 W/m.k 3. Sample quantity: 1 piece per test 4. Sample thickness: total thickness of the sample 35-45mm 5. Sample diameter: hard felt 118mm, soft felt 119mm 6. Testing accuracy: ±3% 7. Repeatability: ≤3%, fully automatic testing analysis software. 8. Heating method: using an 1800W silicon-molybdenum rod heater. 9. The test chamber can be filled with gas and vacuumed. Vacuum degree: 200Pa. Equipment operation: 1. Power on the instrument. After confirming that all cables are correctly connected, turn on the main power switch and rotate the 'power switch' on the instrument. At this time, the power indicator light on the instrument lights up (red indicator), and each instrument performs a self-check. Open the constant temperature water tank, set the temperature to around room temperature, and refer to the cold surface temperature. The display should show a sun, snowflake, and leaf as normal, which can be adjusted by long-pressing the cycle and cooling buttons. Check if the vacuum gauge displays '1 E 5'; if not, the evacuation (inlet solenoid valve) needs to be opened to complete the vacuum in the furnace. 2. Insert the sample. Rotate the 'up-stop-down' knob to open the furnace (the speed of ascent and descent can be adjusted), cut the sample to about 119mm in diameter, and it is best to place it in the sample frame, controlling the thickness within 40-50mm. Rotate the 'up-stop-down' knob to close the furnace. Open the cooling water and constant temperature tank circulating water. 3. Evacuate and fill with protective gas. Rotate the vacuum switch, open the manual vacuum valve (inside the control box), wait until the vacuum displays below 2.0 E 2 (i.e., 200Pa), close the manual vacuum valve, and turn off the vacuum pump. If gas needs to be filled, open the inlet valve, open the gas valve (switch on the gas cylinder or pipeline), adjust the flow, and fill with protective gas. When the pressure gauge approaches atmospheric pressure, open the exhaust valve; the furnace will automatically exhaust when the pressure exceeds atmospheric pressure. 4. Start the experiment. Press the start button, open the instrument software, input the sample thickness (other values can be left blank), and click to start the test. Initially, pay attention to the ammeter reading; if it exceeds 180A (for more than 8 seconds), please long-press the STOP button on the instrument for three seconds, wait ten seconds, and then long-press the RUN button for three seconds. Repeat several times until the ammeter reading is less than 180A. 5. Test data. Once the temperature reaches the desired level, you can click to stop the test, or it can automatically stop when the temperature reaches the termination temperature. After the test, click to save data, which can store the detailed data of this test at the indicated location; click on the test report to open the testing report for this test. In the temperature column, you can input the required temperature point to retrieve the data for this temperature point, and then save the report of this data or directly print this report (a printer must be installed to print; otherwise, only the data report can be saved). Press the work stop button on the instrument panel. If you need to test data under constant temperature conditions: please refer to 'Appendix: Temperature Rise Curve Settings' Table 4.3 settings, and then set the termination temperature in the software to either 1555 or 1558. 6. Save the test report as shown in the figure; you can also modify and create your report style.
Original Article
This article was originally published on our Chinese website. You can view the original version below:
View Original Article →Contact Us for More Information
Have questions about our products or services? Get in touch with our team for expert assistance.
Send us a Message
Contact Information
- Phone
- Office
- Fax
- Address
B6-101, Zhongnan High-Tech Intelligent Manufacturing Industrial Park, No. 10 Shuangma Street, Yuetang District, Xiangtan City, Hunan Province, China
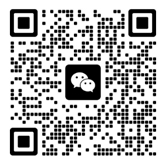